Products |
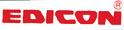 |
|
AVING BREAKERS AND UTILITY
HAMMERS |
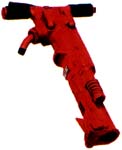 |
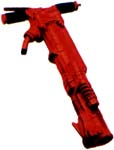 |
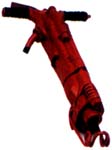 |
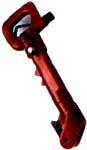 |
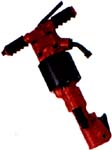 |
EM-23DB |
EM-91DB |
EM-83A |
EM-555UH |
EM-17DB |
|
Features:
-
Forged, heat treated, all
alloy steel construction.
-
Large capacity integral
oil chamber in backhead
-
Muffler available as an
option
-
Forged heavy duty latch
type retainers.
- 4 bolt backhead design on
the DB series.
|
Specification: |
Model |
Net
Weight |
Overall
Length |
Shank |
Piston Dia |
Stroke |
Frequency |
Air
Consumption |
Hose Size |
(kg) |
(lb) |
(mm) |
(in) |
(mm) |
(in) |
(mm) |
(in) |
(mm) |
(in) |
(b.p.m.) |
(m³/min) |
(c.f.m) |
(mm) |
(in) |
EM 83A |
36.0 |
79.2 |
710 |
27
15/16 |
31.7 x
152.4 |
1¼ x 6* |
57.15 |
2¼ |
165.10 |
6½ |
1200 |
2.50 |
88.0 |
19 |
¾ |
EM 23DB |
29.0 |
63.8 |
660 |
25
15/16 |
31.7 x
152.4 |
1¼ x 6* |
60.30 |
2
3/8 |
140.00 |
5½ |
1350 |
1.80 |
63.5 |
19 |
¾ |
EM 91DB |
41.0 |
90.2 |
720 |
28
3/8 |
31.7 x
152.4 |
1¼ x 6* |
66.68 |
2
5/8 |
158.00 |
6¼ |
1250 |
2.40 |
84.5 |
19 |
¾ |
EM 17DB |
18.0 |
40.0 |
533 |
21 |
25.0 x
108.0 |
1 x
4¼ |
48.00 |
1
7/8 |
124.00 |
5 |
1450 |
1.36 |
48.0 |
19 |
¾ |
EM 555UH |
9.0 |
20.0 |
550 |
21
2/3 |
22.0 x
82.0 |
7/8 x
3¼ |
40.00 |
1
9/16 |
88.00 |
3
7/16 |
1500 |
1.25 |
44.0 |
19 |
¾ |
|
* 28.6 mm x 152.4 mm, 1 1/8 x
6" shank availableSince improvements are made
from time to time, specifications may change without
notice. |
Top |
Chisel / Needle
Scalers |
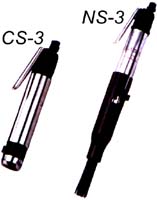
|
Features:
-
All parts from Heat treated
alloy steel.
-
Replaceable chisel bushing
for economy
-
Front exhaust cleans work
surface
- 3 position needle tube
adjusts as needles wear.
|
|
Specifications: |
Model |
Net
Weight |
Overall
Length |
Shank |
Piston Dia |
Stroke |
Frequency |
Air
Comsumption |
Hose Size |
(kg) |
(lbs) |
(mm) |
(in) |
(mm) |
(in) |
(mm) |
(in) |
(mm) |
(in) |
(b.p.m.) |
(m³/min) |
(c.f.m) |
(mm) |
(in) |
CS-3 |
1.70 |
3.75 |
238 |
9 1/8 |
12.7 |
0.500 |
25.4 |
1 |
28.6 |
1 1/8 |
4600 |
0.34 |
12 |
8 |
5/16 |
NS-3 |
2.70 |
6.00 |
432 |
17 |
12.7 |
0.500 |
25.4 |
1 |
28.6 |
1 1/8 |
4600 |
0.34 |
12 |
8 |
5/16 |
|
Since improvements are made from time to
time, specifications may change without
notice |
Top |
Chipping Hammer and
Rivet Busters |
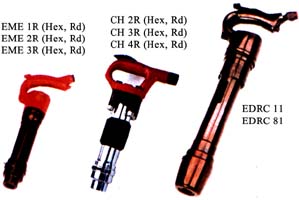
|
Features:
- Forged, Heat treated steel
construction.
-
Alloy steel heat treated
& precision ground components.
-
Quick and secure chisel
retention.
-
A vareity of accessories are
available for the Chipping hammer
- Available in different
strokes for different needs.
|
|
Specifications: |
Model |
NetWeight |
OverallLength |
Shank |
PistonDia |
Stroke |
Frequency |
AirConsumption |
Hose Size |
(kg) |
(lbs) |
(mm) |
(in) |
(mm) |
(in) |
(mm) |
(in) |
(mm) |
(in) |
(b.p.m) |
(m³/min) |
(c.f.m) |
(mm) |
(in) |
EME 1R |
6.33 |
13.9 |
362 |
14¼ |
Round 17.27Hex 14.70 |
0.6800.580 |
28.60 |
1 1/8 |
25.40 |
1 |
2850 |
0.75 |
26.5 |
12.7 |
½ |
EME 2R |
6.73 |
14.8 |
377 |
14 7/8 |
Round 17.27Hex 14.70 |
0.6800.580 |
28.60 |
1 1/8 |
50.80 |
2 |
2500 |
0.83 |
29.3 |
12.7 |
½ |
EME 3R |
7.33 |
16.1 |
427 |
16 7/8 |
Round 17.27Hex 14.70 |
0.6800.580 |
28.60 |
1 1/8 |
76.20 |
3 |
2050 |
0.90 |
31.8 |
12.7 |
½ |
CH 2R |
7.33 |
16.1 |
356 |
14 7/8 |
Round 17.27Hex 14.70 |
0.6800.580 |
28.60 |
1 1/8 |
76.20 |
3 |
2300 |
0.74 |
26.0 |
12.7 |
½ |
CH 3R |
7.84 |
17.2 |
387 |
15¼ |
Round 17.27Hex 14.70 |
0.6800.580 |
28.60 |
1 1/8 |
95.30 |
3¼ |
2100 |
0.82 |
29.0 |
12.7 |
½ |
CH 4R |
8.24 |
18.1 |
419 |
16½ |
Round 17.27Hex 14.70 |
0.6800.580 |
28.60 |
1 1/8 |
108.0 |
4¼ |
1700 |
0.93 |
33.0 |
12.7 |
½ |
EDRC 81 |
14.0 |
30.8 |
584 |
23 |
Round 17.27Hex 14.70 |
0.6800.580 |
30.16 |
1 3/16 |
203.2 |
8 |
1200 |
1.00 |
35.3 |
12.7 |
½ |
EDRC 11 |
15.5 |
34.1 |
660 |
26 |
Round 17.27Hex 14.70 |
0.6800.580 |
30.16 |
1 3/16 |
280.0 |
11 |
800 |
1.10 |
38.8 |
12.7 |
½ |
|
Since improvements are made from time to
time, specifications may change without
notice |
Top |
Air Tool & Line
Accessories |
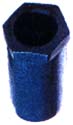 |
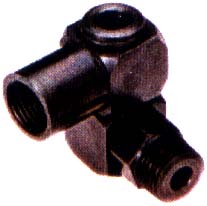 |
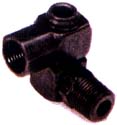 |
Air Line
Filters |
Air Swivel Assembly (1/2"
NPT) |
Air Swivel Assembly (3/8"
NPT |
|
|
|
 |
Needle |
|
|
|
 |
Chisel
End |
|
Moil Point |
|
|
|
Since improvements are made from time to
time, specifications may change without
notice |
Top |
EDICON PNEUMATIC TOOL
SPARES LIST |
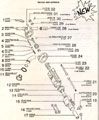
CLICK FOR IT'S FULL VIEW |
|
Safety
Checks
- Continued prolonged use may
lead to gradual loss of hearing. Wear suitable ear protection and
operate the tool with a muffler.
- Wear safety goggles to
protect eyes against flying particles.
-
Keep hoses in good condition. Check hoses for signs of wear and ensure that fittings are
secure. Accidental disconnection while hose is pressurized can
make the hose whip and can be a safety hazard.
- To avoid Injury from ejected
steel, Replace worn or broken parts to maintain proper steel
retention. Ensure that chisel is secured. Check latch mechanism
fur correct locking.
- Do not operate tool with
chisel without first engaging chisel against the' job.
- Safety shoes are recommended
to protect feet during operation.
AIR
REQUIREMENTS
All Edicon demolition tools
require air at a steady 80-90 PSIG (5.6-6.3 bar) pressure. The air
should be clean (filtered) and dry (moisture free).
The pipes and/or hoses leading
to the tool should be of the minimum recommended diameter. For the
EM83A/EM-83AS breaker the size is 3/1111 Internal diameter.
We recommend an air line
separator to remove moisture which Is usually present in air lines.'
Also it is Important 'to have a filter to remove any particles.
These air line accessories should be as close to the tools as
operation will permit.
The EM83A/EM-83AS breaker
consumes 88 CFM of air in continuous operation. Normal use is
intermittent, so the average consumption will be lower than 88 CFM,
the extent depending upon the type of usage. However always make
sure that there is more than 88 CFM available on the air line by
checking output of compressor and number of connected, operating,
tools.
LUBRICATION
REQUIREMENT:
A) Quantity
Always ensure that a
Line-Lubricator is Installed on the air-supply Line as, close as possible to the
tool, and that the discharge rate is adequate. It is also recommended to top up
the in built oil chamber on the handle of the tool as and when
required (every shift)
One practical way to test if
the tool is receiving enough oil is the presence of oil mist in the
tool exhaust. The presence of this mist can be checked by holding a
surface (ones hand) in the exhaust during operation, if the surface
appears oily than the lubrication rate is adequate.
Another simple test is to see
if the shanks of chisels being used appear oily and if they are, it
indicates adequate lubrication.
B) Quality of Lubrication
|
Recommended Oil for EM83A/
EM83AS Breakers is any of the following. |
Manufactured By - |
1) SPINTEK-22
2) BHARAT HYDROL-22
3) SERVOSPNY 22
4) CASTROL HYSPIN AWS-22
or equivalent. |
Hindustan Petroleum
Bharat Petroleum
Indian Oil
Indrol |
|
DO’S AND DON’TS
- Daily blowout hoses and
ensure hoses are in good condition and clean.
- Pour in an ounce of oil
into the air inlet before connecting hoses.
-
Do not operate tool without
the chisel being in contact with the work.
-
Ensure chisels are in top
condition, i.e_ well sharpened.
-
Retighten bolts on the
breaker to recommended torques frequently.
-
When not in use, plug
openings to avoid ingress of dirt.
-
Observe safety
precautions.
-
Never operate at pressure
over 90 PSIG (6.3 bar).
|
|
Maintenance - |
If the tool is being used
extensively, it is strongly recommended to fix up a regular
preventive maintenance programme. The tools are very simple to
dissemble/resemble and we recommend that the tools is dismantled
completely and parts checked for wear or damage and replaced
accordingly . |
|
HOW DO DISASSEMBLE AND
RE-ASSEMBLE EM-83A/EM-83AS
Disassemble breaker by opening
up the front head and back head boltstaking care to see that the
components are not damaged by scoring andcareless handling. |
|
Check the
following
A) Check for scoring or damage
to internal components.
B) Check valve parts and valve
action.
C) Check anvil block, if there
is distortion at the ends, replace.
D) Check retainer
action.
Thoroughly clean oil parts,
replace worn/damaged parts and re-assemble as follows:
1) Before assembly, coat all
parts with recommended Oil.
2) Pull up back head bolts
(22) evenly by alternating from 'one to the other to distribute the load and to minimize bolt failure.
Torque 125-150 ft.lbs.
3) Draw up front head bolts
(21) alternatively, a little at a time,compressing springs (29)
evenly. When springs bottom, loose .bolts ½ to 1 turn.
Assemble length 2 3/8" - 2
5/'16".
4) Install air inlet swivel
(8) and tighten nut (11) to 125-150 ft.lbs. torque. Be sure "0"
Rings (9 & 10) are in position.
5) When assembly is complete,
fill oil chamber and tighten oil plug (32) to 80-100 ft.lbs. torque.
Pour about 1/2 Oz. Recommended Oil into air inlet swivel (8) and
operate tool ON REDUCE THROTTLE FOR 10-15 seconds.
|
Top |