 |
Multi Service
Govt. Contractor & General Supplier |
|
Specialist in All Type of Civil, Mechanical (Boiler & Turbine Auxiliaries), Erection & Maintenance Electrical, Insulation, Refractory and AC works etc. |
|
|
|
Mechanical Division
1) Boiler & Turbine Auxiliaries
Boiler Operation and Maintenance. Each year, hundreds of accidents are reported nationally involving steam and hot water heating boilers. Most are attributed to malfunctioning low water cutoffs, operator error, poor maintenance and/or corrosion. Properly functioning control or safety devices are absolutely essential.
We provide full scope maintenance services for steam and gas turbine and generator units including their mechanical and electrical auxiliary systems, and control and protection systems. We offer long-term service agreements for all services provided.
|
|
|
2) Cooling Tower
Cooling tower maintenance including Gearbox servicing and replacement of blades, Driving shaft replacement, valve servicing, Sludge pump overhauling, Hot basin cleaning and servicing. |
|
|
3) BFP (Boiler Feed Pump)
Most “wear and tear” damage occurring to feed systems and their components is caused by corrosion resulting from leaking external pipe joints. Look over the system frequently and repair any piping leaks and resultant corrosion damage immediately.
Refer to the pump manufacturer’s instruction manual fordetailed maintenance procedures. Generally, the only maintenance work required is occasional bearing lubrication or seal replacement. For more extensive repairs, pump replacement may be required. In some cases, service exchange pumps are available from the pump manufacturer. |
|
|
4) Repairing & Reconditioning of Pumps / Gear boxes (ACW, CCW, BFP, Water line)
We have good & experience team for Overhauling, Balancing of Rotating Assembly, Pump Spare Supply & Alignment of Pump with Motor |
|
|
5) Repairing & Reconditioning of all types Valves (Safety, Gate, Globe, NRV, MOV, Control)
Multi Service has the capability to make a repaired gate, globe, or check work better than it did when it was new. Size is not an issue. Multi Service can repair any size gate, globe, or check valve.
Multi Service can repair any type of butterfly valve, to standard lined butterfly valves, to high performance butterfly. Size is not a factor. Multi Service regularly gets in valves for repair in the 64" rang.
Multi Service can repair any type of ball valve from small 1" ball valves up to this 24" Grove ball valves and even larger. Metal seated and ceramic seated ball valves are no problem for Multi Service.
Multi Service has the capability to repair any brand of control valve.
We can repair safety valves in your plant. Large or welded-in safety and safety relief valves can be repaired in place. |
|
|
6) Online Leak Sealing in Running Plant
A) STANDARD APPLICATIONS :
• Bolted Flange / Gasket Leaks
• Leaks from Pipes and Piping Components
• Leaks from Valve Glands
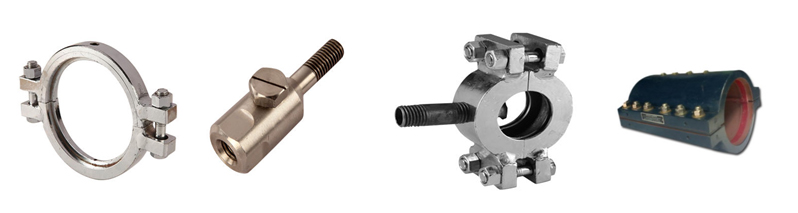
B) DEFECT TYPES & FAILURE MECHANISMS ADDRESSED :
• Local wall thinning, pitting, blisters, pinholes, etc.
i) Note that for very extensive wall thinning, composite repair may be the more appropriate repair technique
ii) External Corrosion
- Environmental corrosion
- Crevice corrosion
- Galvanic corrosion
- Corrosion under insulation (CUI) / Under lagging corrosion (ULC)
- Corrosion under pipe supports
iii) Internal Corrosion / Erosion / Erosion assisted Corrosion
- Leak sealing repair will not prevent further propagation of the defect
- Full extent of the defect is not obvious and may be much more extensive that it would appear
• Cracks
i) Weldments, Heat Affected Zone (HAZ) and Parent Metal
ii) Special care is required for the repair of cracks, which have the possibility to propagate very rapidly
- Longitudinal cracks may propagate beyond the bounds of the repair
- Circumferential cracks may propagate to cause complete pipe separation inside the repair
• Mechanical Damage
i) Dents
ii) Gouges
iii) Note that enclosures over non through-wall defects, will need to filled with hard setting resin or grout, if they are to provide hoop reinforcement to the enclosed pipe
• Leaks at Gaskets
i) Incorrect gasket selection
ii) Incorrect stud pre-load
iii) Flange misalignment
iv) Gasket seating face defects
• Leaks at Gland Seals
i) Scored spindles
ii) Corroded spindles
|
|
|
• Our solutions maintain the integrity of your process systems.
• Keeping systems on-line reduce the amount of potentially harmful and polluting fugitive emissions released into the atmosphere.
• Our goal is to extend the life of your plant components. ‘Repair rather than replace’ enables you to avoid the unnecessary re-manufacturing and replacement of equipment |
|
|
|